The growing concerns over the potential safety hazards of vertical tippers are making people think more about the alternatives. There are many news stories out there today informing us of the potential dangers and consequences of the misuse of vertical tippers. Having acknowledged the risk, let’s turn our attention to the positive side and consider the alternatives. If we look at the generic horizontal ejector systems, there are several options available.
These include moving floor, push out, and belt driven systems.
Moving floor systems are a hydraulically-driven moving floor conveyance system ideal for moving bulk material or palletized product; however, they do not fare so well with finer aggregate loads such as limestone dust or sand due to the potential ingress of material acting as an abrasive within the moving parts. In some cases, the moving floor system can also be used to automate and facilitate the loading of palletized goods, eliminating the need for a forklift. Moving floor systems can take approximately 5 to 15 minutes to unload a full 13.6-metre trailer, depending on the material being discharged. Some users of the moving floor system have observed that its operation can be noisy, and this may be important when operating in an environment sensitive to disturbance from noise.
Push out ejector systems utilise a three-stage telescopic cylinder. This cylinder extends and pushes the aggregate load to the rear of the vehicle. Owner/ operators have reported that the system works well overall, successfully ejecting a range of aggregate loads in around 5-12 minutes. Maintaining the sequence of discharge is important to the operation of this system.
Belt driven systems use a conveyor belt system to carry loads towards the rear of the truck. This system has the least moving parts, making it easy to maintain. Different belts can carry a wider range of materials than the walking floor and push out systems, as there are no gaps for finer aggregate material to fall into. Out of the three mentioned, belt driven systems operate quieter, quicker and more efficiently, but all this comes at a price.
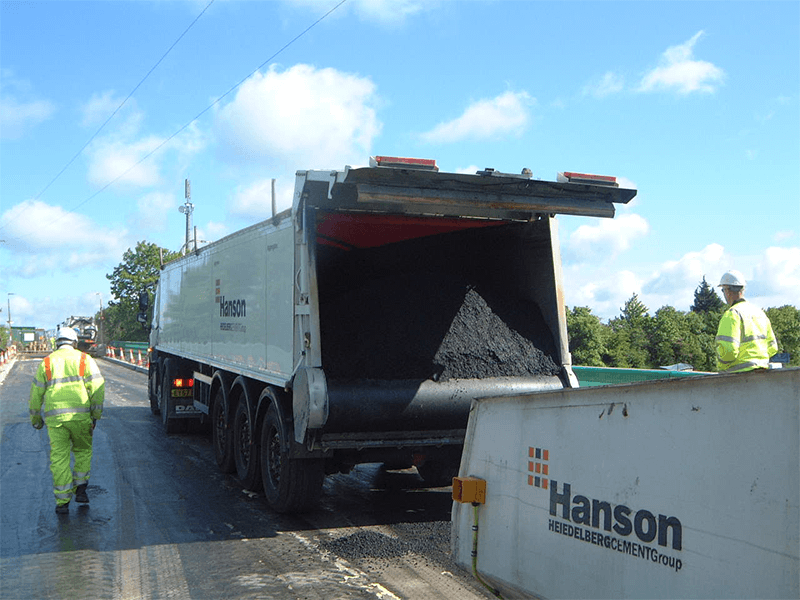
The main influences affecting a business’s decisions to include a horizontal ejector system-based vehicle are the increasing number of Zero Harm contracts being awarded, the environmental benefits, low maintenance costs, and the health and safety of the work force.
For these reasons the use of vertical tippers are slowly becoming reduced across construction sites. An example of these conditions being put into place is at the construction site of Hinkley Power Station in Somerset. Here, they are very sensitive to the potential problems of aggregate loads being discharged through tipping, and the use of the Multidrive horizontal ejector system (HES) is acknowledged as a more widely acceptable alternative.
Every construction site around the world makes an impact to their surroundings to a greater or lesser degree, including wildlife habitat, neighbours, and the natural and built environment. Good environmental practise enables these impacts to be managed positively. Impacts can take many forms. The most obvious ones are those that affect flora and fauna, watercourses, noise, and pollution. Vertical tippers are renowned for having a more negative affect on these aspects. The dust cloud produced when tipping can adversely affect the flora, fauna, and pollution levels. This has become a major influence when deciding to make the move to horizontal. If environmental considerations are the carrot, then penalties arising from the misuse of tippers may be the stick.
Recently, the Mick George Haulage Company was fined £565,000 when a vertical tipper came “close to touching” an overhead line. As a consequence, companies are weighing up the pros and cons of all types of discharge systems more seriously than may have been the case in the past.